鋳造・加工・組立までの一貫生産体制により、
高品質でコストを抑えた製品づくりを行っています。
鋳造
高品質な製品作りの要となる最初の工程
ダイカスト用アルミ合金を溶解炉で溶かし、ダイカストマシン内の金型へ溶けたアルミを高速・高圧で充填することで製品を成形します。
成形した製品はロボットで取り出され、バリ除去等の仕上げや各製品に応じた品質検査を実施し粗材を完成させます。
金型に充填したアルミの流動解析や蓄積した経験・ノウハウを基にした鋳造条件の設定および金型メンテナンスを継続的に行うことで安定した品質を維持しています。
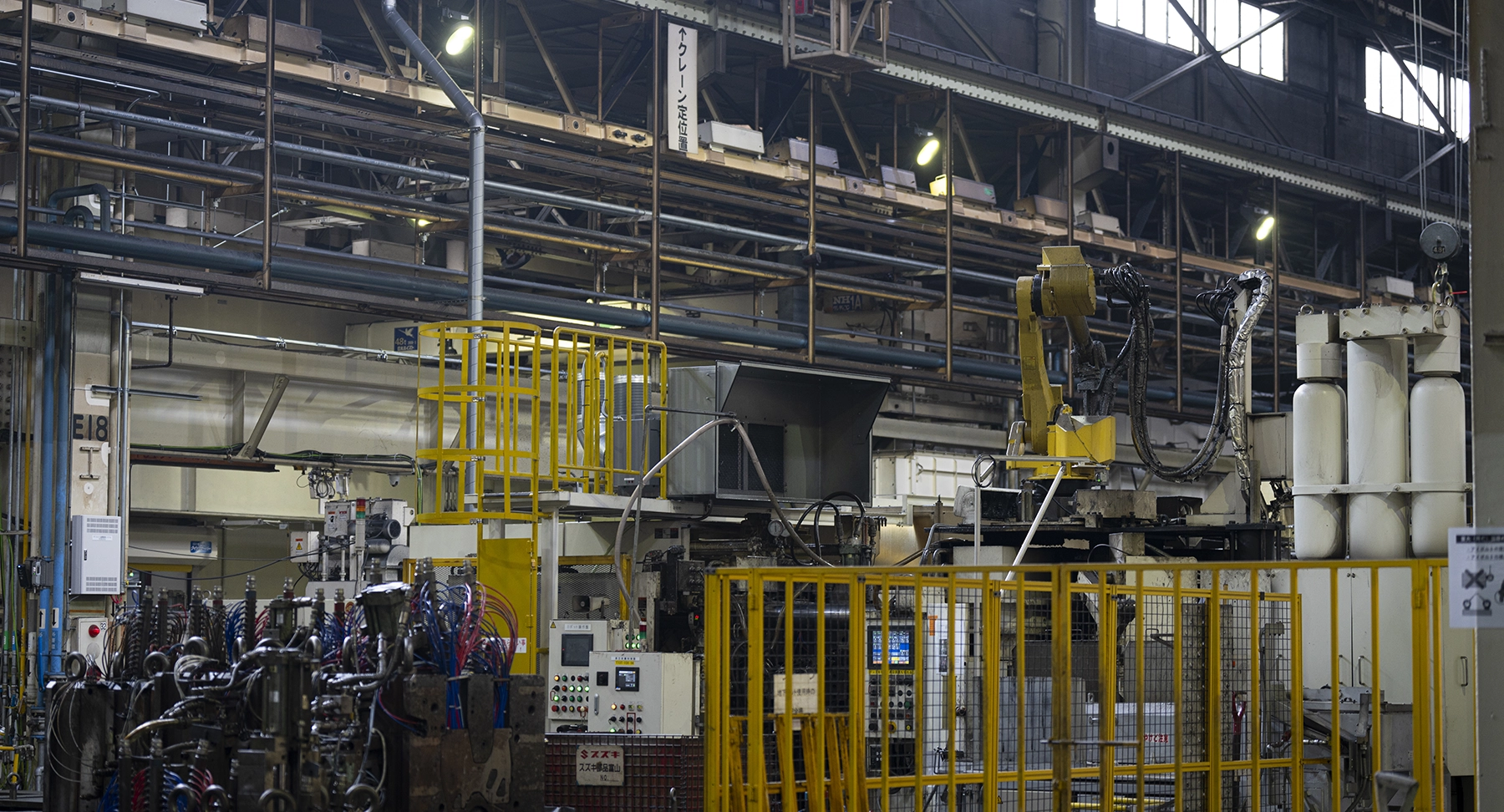
加工
自動化による生産性向上
マシニングセンタ等を使用し、鋳造した粗材にフライス削り、中ぐり、穴あけ、ねじ立て等の切削加工を行います。
生産台数の多い製品は、ロボットを活用しバラ積みからの粗材取り出し、加工、洗浄、検査、払い出しまで全て自動搬送することで省人化、生産性向上を図っています。
また従来、人が目視で行っていた外観検査を画像認識技術を用い自動化し、人為的なミスを削減し品質の安定化を実現しています。
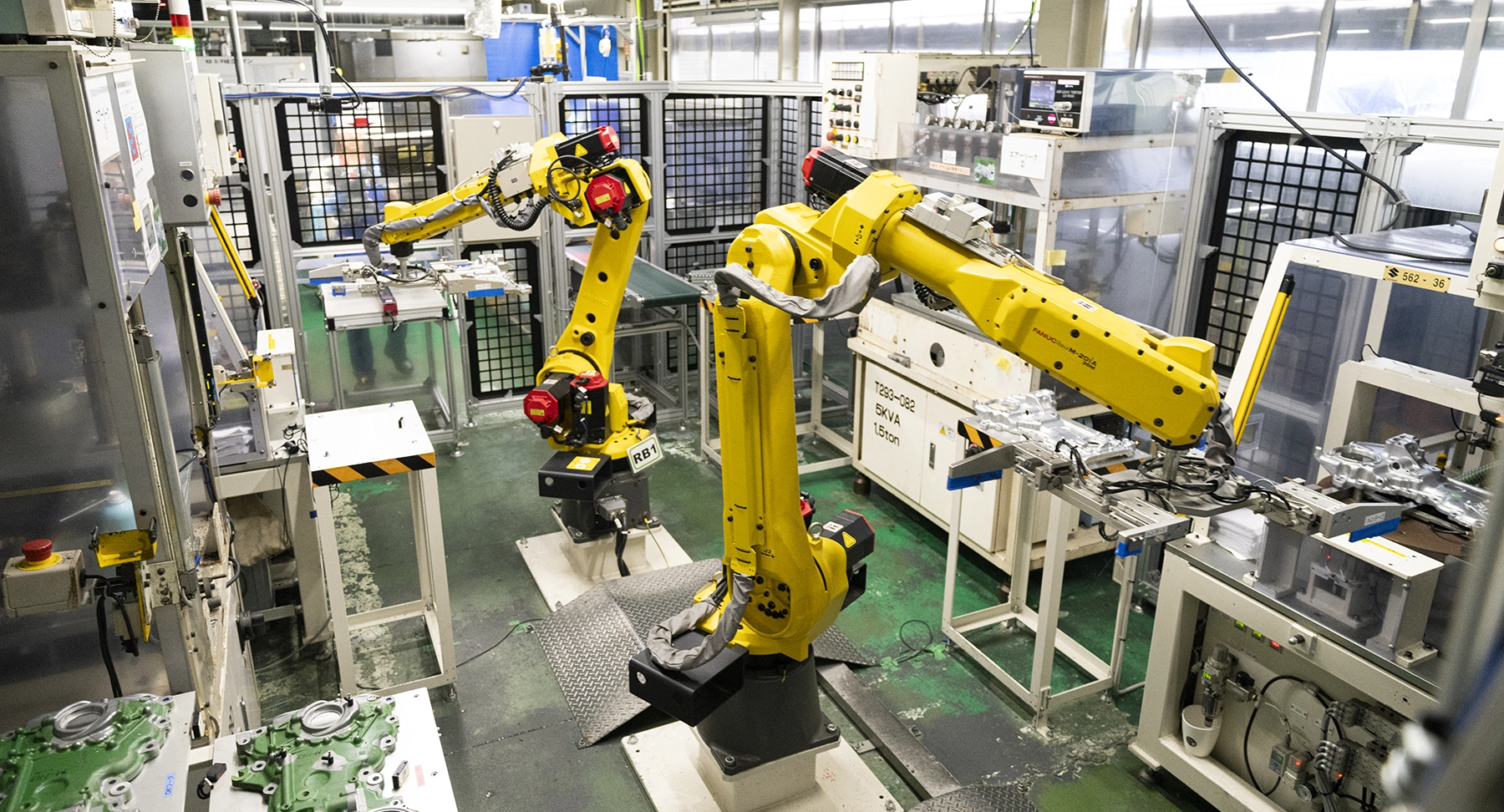
組立・検査
人にやさしいラインづくり
加工した製品にネジ締め機や圧入機等を使用し部品を組み付けし、リークテスト、外観検査を行ない完成品へと仕上げます。
「小・少・軽・短・美」の考えのもと、歩行距離削減、無理な姿勢の作業を無くすなど動作のムダを排除する継続した改善活動を 通じて、作業者が効率良く安全に作業ができる人にやさしいラインづくりを行っています。
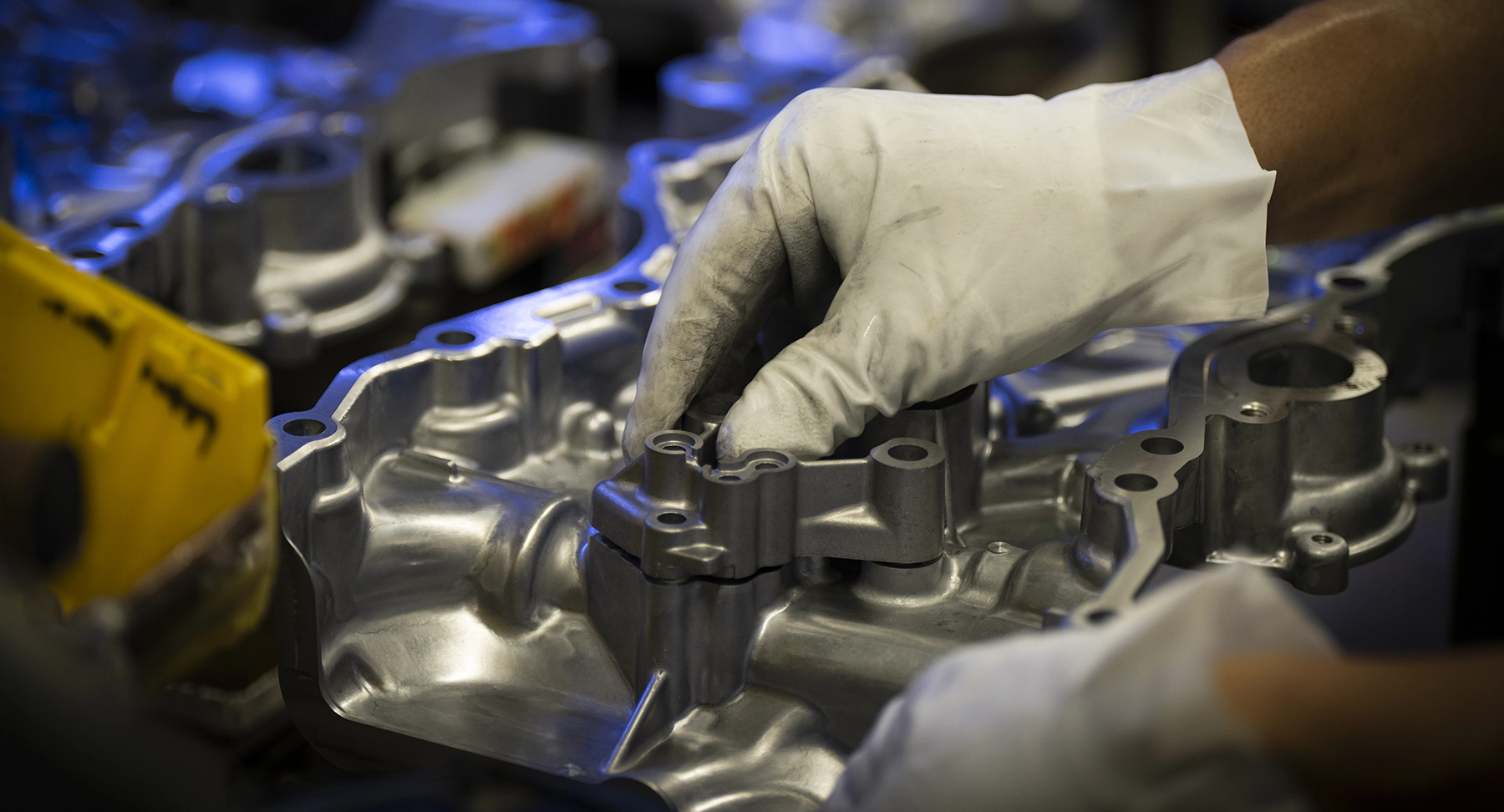